The fundamental goal of any respiratory
protection program is to control occupational
diseases caused by breathing air contaminated
with harmful dusts, fogs, fumes, mists, gases,
smokes, sprays, and/or vapors. The defense
against these contaminants is simple: Keep
them out of the air that workers breathe. Always implement engineering and/or
administrative controls first. If contaminants still present a hazard, you must
provide appropriate respiratory protection for every employee who might be
exposed to them.
MSA can help you take a comprehensive
approach to sound Respiratory Protection
practices. This guide will help you understand
the need for respirators, how they work, and
what their limitations are.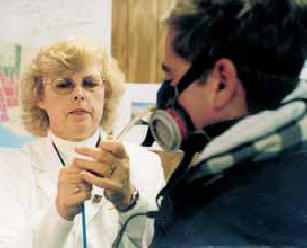
OSHA (the Occupational Safety and Health
Administration) and
NIOSH (the National Institute of Safety and Health) regulations define all the
specific requirements which must be followed, including the capabilities of
appropriate respiratory protection. Employers must follow the requirements of
these governmental regulations, both the general regulations which apply to all
workplaces and the specific regulations for exposures in their particular
industry, such as lead, silica dust, asbestos, and benzene.
A Written
Respiratory ProtectionProgram
Administration
The first step in a
respiratory protection program is to establish written standard operating
procedures governing the selection and use of respirators.
Regular inspection and
evaluation of the
program will ensure its
continued effectiveness.
According to OSHA, a
written program will help employers, employees,
and compliance officersgauge the adequacy of a
given program. When developing your written
respiratory protection program, be sure to
include the following elements, designated by
29 CFR Part 1910.134: |
|
• Procedures for
selecting respirators for use in
the workplace
• Fit-testing
procedures for tightfitting respirators (including a signed copy of
employees’ fit-test records)
• Procedures for
proper use of respirators in
routine and
emergency situations
• Procedures and
schedules for cleaning,
disinfecting,
storing, inspecting, and repairing
respirators
• Procedures to
ensure adequate air quality,
quantity, and flow
of breathing air for atmos-pheresupplying respirators
• Medical
evaluations of employees required to
wear respirators
Employers must:
• Submit a written
respiratory protection
program unless the
choice of voluntary
respiratory
protection is a filtering facepiece
(dust mask)
• Provide voluntary
respirator users with
Appendix D (p. 1284)
of the Standard
• Ensure that
employees using a respirator
voluntarily have
medical clearance
Employees must
clean, store, and maintain the
respirator so that
its use does not present a
health hazard.
Voluntary Respirator
Use
An employer must
provide respiratory protection for employees who ask for it or let employees
use their own respiratory protection, if such respirator use will not create
a hazard. Fit testing is not required for voluntary use.
If possible, one
person should administer these
procedures, to
ensure consistent coordination
and direction and
optimum results. The actual
respiratory
protection program itself for each
workplace depends
upon many factors, and may require input from specialists such as safety
personnel, industrial hygienists, health physicists and physicians.
Respiratory Hazards
Before a respiratory
protection program is
initiated, it is
important to first understand the
types of respiratory
hazards inherent to your
industry. Of the
three normally recognized ways
toxic materials can
enter the body—through the
(1) gastrointestinal
tract, (2) skin, and (3) lungs— the respiratory system presents the quickest
and most direct avenue of entry. This is because of the respiratory system’s
direct relationship with the circulatory system and the constant need to
oxygenate tissue cells to sustain life.
The three basic
classifications of respiratory
hazards are:
• oxygen-deficient
air
• particulate
contaminants;
• gas and vapor
contaminants. |
|
The 7 Key Elements
Chances are that you
are already
familiar with the
need for and use of
respirators in your
workplace, but
as with anything
else, it doesn’t hurt
to review your
current program
against standard
operating
procedures governing
the selection
and use of
respirators. According to
program details in
OSHA’s
Respiratory
Protection Standard
(29 CFR 1910.134),
the seven key
elements that every
respiratory
protection program
should
contain are:
1.
A written
plan detailing how the
program will be
administered
2.
A complete
assessment and
knowledge of
respiratory
hazards that will be
encountered
in the workplace
3.
Procedures
and equipment
to control
respiratory hazards,
including the use of
engineering
controls and work
practices
designed to limit or
reduce
employee exposures
to such
hazards
4.
Guidelines for the
proper
selection
of appropriate
respiratory
protective
equipment
5.
An employee
training program
covering hazard
recognition,
the dangers
associated with
respiratory hazards,
and proper
care and use of
respiratory
protective equipment
6.
Inspection,
maintenance, and
repair
of respiratory
protective
equipment
7.
Medical
surveillance
of
employees
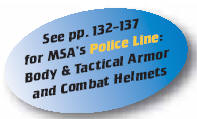 |